Сварные соединения делятся на несколько видов: торцовые, нахлесточные, угловые, тавровые и стыковые. Последний вид сварки — это соединение двух деталей, примыкающих друг к другу торцевыми поверхностями. При УЗК сварки могут быть выявлены несоответствия изделий требованиям, прописанным в нормах ГОСТ. Такие несоответствия принято называть дефектами (повреждениями).
Чтобы исключить дефекты, возникающие при сварке стыковых соединений ответственных конструкций, специалисты компании «НДТ-Контроль» используют среди прочих метод УЗК. Это вид неразрушающего контроля на присутствие повреждений в виде несплошности и неоднородности. Он незаменим при выявлении недостатков сварочных швов в различных материалах и изделиях, находящихся на большой глубине. Используется в энергетическом и химическом машиностроении, нефтяных и газовых отраслях, железнодорожном транспорте, судостроении. Для контроля применяются продольные (когда ультразвук нужно ввести перпендикулярно или под малым углом) и поперечные (когда угол большой) волны. К ультразвуковому контролю сварных стыков согласно ГОСТу относятся несколько методов УЗК. Дефект при их использовании обнаруживается быстро.
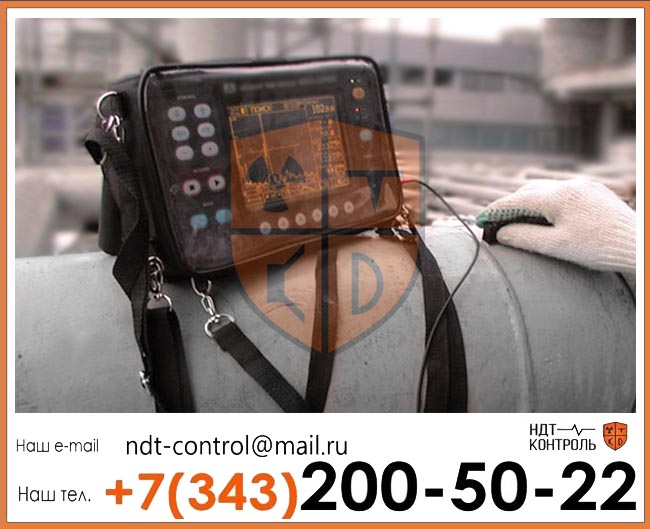
Эхо-метод
Эхо-метод основывается на приеме отраженной волны от участка с повреждениями и характеризуется высокой чувствительностью при одностороннем доступе, точностью определения повреждения. Но он не устойчив к внешним препятствиям, из-за чего могут возникнуть погрешности. 90% всех дефектов сварных стыков толщиной более 4 мм при одностороннем доступе выявляются именно этим методом.
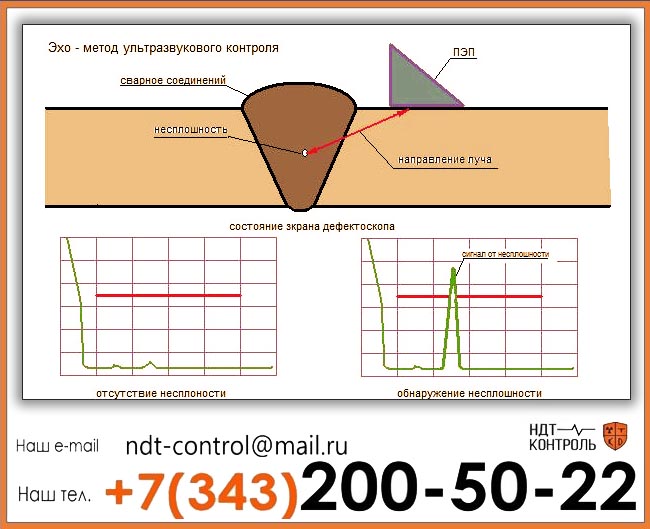
Теневой и зеркально-теневой методы
Теневой метод УЗК сварных стыков строится на изменении ультразвуковых колебаний при выявлении повреждения. Чем больше участок с дефектами, тем ниже амплитуда колебаний, дошедших от дефекта до приемника. Амплитуда обратно пропорциональна размеру повреждения. Для использования этого способа необходим двусторонний доступ к конструкции. Кроме того теневой метод менее чувствителен, поэтому с помощью него трудно определить точные координаты поврежденного места. Но есть и преимущества:
- большая устойчивость к внешнему шуму;
- низкая зависимость колебаний волны от ориентации повреждения;
- обнаружение наклонных повреждений, не отражающих прямых волн.
Зеркально-теневой метод основывается на уменьшении колебаний сигнала, отходящего от донной поверхности при обнаружении повреждения. Преимуществом зеркально-теневого метода является односторонний доступ и более высокая чувствительность к повреждениям внизу шва. При оценке сварных стыков металлоконструкций используются оба этих УЗК. Образец работы приборов с помощью этих методов наши специалисты продемонстрируют при заявке клиента.
Эхо-зеркальный метод
Эхо-зеркальный метод «тандем» незаменим для выявления плоскостных вертикальных поражений. В этом случае шов исследуется 2 ПЭП. Один из них отражает сигнал, другой принимает излученный и дважды отраженный от участка с дефектами сигнал. Главным преимуществом эхо-зеркального метода является способность оценки разновидности дефектов больше 3 мм, отклоненных менее чем на 10% от вертикальной плоскости. «Тандем» из-за своей надежности в определении вертикально-ориентированных дефектов используется при контроле сварки изделий с толстыми стенками.
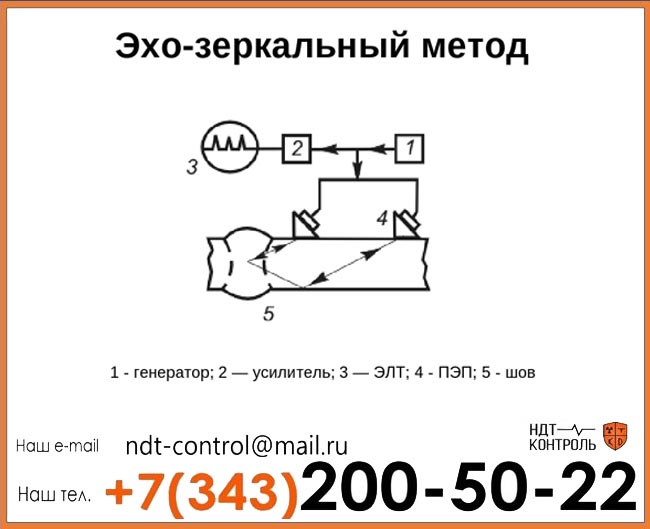
Дельта-метод
Дельта-метод при исследовании использует ультразвук, отраженный повреждением. Прибор улавливает продольный и частично дифрагированный звук. Сложность применения этого метода состоит в трудности расшифровки принятых волн при оценке стыков менее 15 мм. При использовании этого типа УЗК шва вначале зачищают стык, и только потом начинают проверку.
Выбор методов УЗК зависит от толщины сварочных стыковых соединений, от типа сварки (плавление или давление) и доступа преобразователя к участку повреждения.
УЗК контроль сварных стыков небольшой толщины производится сегодня с помощью современных ультразвуковых дефектоскопов. Принцип их работы основан на способности ультразвуковых волн проникать в металл и отражаться от поврежденной поверхности. Таким образом, колебания доходят до сварного соединения и при выявлении дефекта отклоняются от пути. Дефектоскоп улавливает малейшее колебание и определяет размер поврежденного участка и характер дефекта. Заключение УЗК прописывается в журнал контроля.
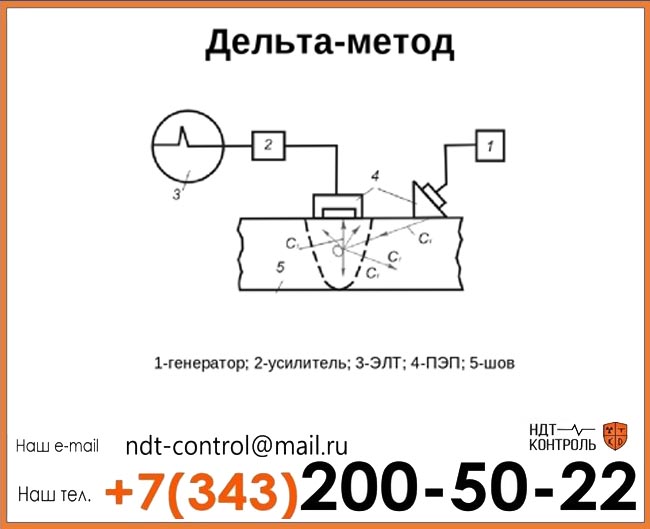